7075 T6 6061 6082 forged aluminum manufacturer,AL 7075-T651 FRAME CNC machining, Aluminum alloy forgings supplier,brass aluminum forge enterprises,anodized aluminum forging companies, ISO TS 16949,IATF16949,
Aluminum Forgings Suppliers,Aluminum alloy CNC machining parts,Magnesium alloy/brass Aluminum/Copper forged parts OEM factory,7075 T6,6063,6082,6061 hot forgings/Cold forged process, quality Aluminum forged accessories,
Forged Aluminum Alloy Advantages
Because of its strength, aluminum forgings remain ideal for applications where performance and safety are a high priority as it can endure intense conditions for a wide variety of industries, including Aerospace, Semiconductor, Defense and Marine.
Benefits of Forged Aluminum
Strength to weight ratio, Light weight/low density, Corrosion resistance ,High thermal conductivity, Design flexibility, Good surface finish ,Fracture toughness, Fatigue and fatigue crack growth ,Cryogenic properties
Aluminum alloy Grades:
2011-T3 | QQA-225/3 |
2014 | AMS4028 |
2014-T6 | AMS4121, QQ-A-225/4,QQ-A-200/2 |
2014-T651 | AMS4029 |
2024-T351 | AMS4119, QQ-A-225/6,QQ-A-200/3 |
2024-T4,T351 | AMS4120, QQ-A-225/6,QQ-A-200/3 |
2024-T6 | AMS4112, QQA-225/6, QQ-A-200/3 |
2219 | AMS4031, AMS4066, AMS4068, AMS4094, AMS4095 and AMS4096 |
5052-F | AMS4114, QQA-225/7 |
5083 | QQA-200/4 |
5086 | QQA-200/5 |
6061-0 | AMS4115, QQA-225/8, QQ-A-200/8 |
6061-T451 | AMS4128, QQA-225/8, QQ-A-200/8 |
6061-T4 | AMS4116, QQA-225/8, QQ-A-200/8 |
6061-T6, T651 | AMS4117, QQA-225/8, QQ-A-200/8 |
6063 | QQA-200/9 |
6262 | QQA-225/10 |
7050-T7451 | AMS4050 ASTMD-2154 |
7075-T6 | AMS4122, QQA-225/9, QQ-A-200/11 |
7075-T651 | AMS4123, QQA-225/9, QQ-A-200/11 |
7075-T7351 | AMS4124, QQA-225/9, QQ-A-200/11 |
7150-T6151 | BMS7-256 |
7150-T77511 | AMS4252, BMS7-306 |
7178 | QQA-200/13 |
7175 7075 Aluminum forgings forged product parts
7175 improves the purity of 7075 alloy. It is mainly used as die forgings. It has three heat treatment states: T66, T74 and T7452. Among them, the static strength of T66 forging is higher than that of 7075 T6 forging, while fatigue, crack resistance and stress corrosion resistance are equivalent. The static strength of T74 die forging and free forging is similar to that of 7075 T6 forging, and the stress corrosion resistance balance is between 7075 T73 and 7075 T76, while the toughness and fatigue properties are comparable to or even better than 7075 T73 forging. The stress corrosion resistance of T74 state is obviously higher than that of 7075 T6 state, approaching 7075 T73 state.
7175 alloy is specially used to produce forgings and rolling rings. The material state is T74. The characteristics of 7175 T74 aluminium alloy forgings are that special processing and heat treatment processes are adopted to make the strength close to 7075 T6 alloy forgings and the stress corrosion resistance close to 7075 T73 forgings in the best corrosion state. The reduction of Fe and Si rolling can not only improve the forging properties of the alloy, but also significantly improve the stress corrosion resistance and fracture toughness of the forgings.
7075 aluminium forgings are high strength deformed aluminium alloys strengthened by heat treatment at any time. They can produce products of various kinds and sizes. They are the most widely used high strength aluminium alloys at present. It has several heat treatment states: T6, T73 and T76. The strength of T6 state is the highest, but the fracture toughness is low.
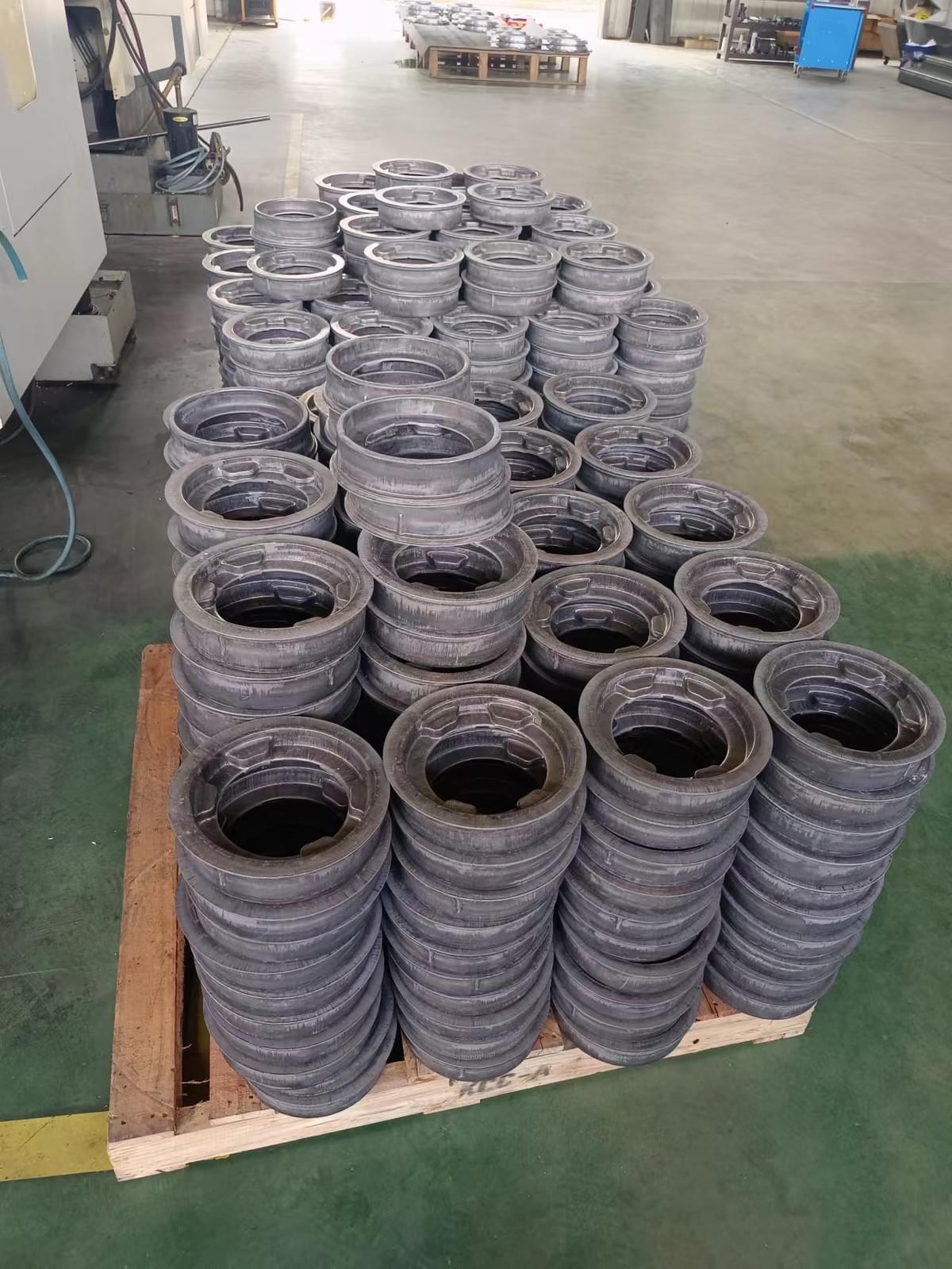
7075 Aluminum Forging
Aluminum 7075 is a zinc, copper, and magnesium containing alloy capable of superior strength and stress corrosion cracking resistance. AL 7075 is an excellent material for use in highly stressed structural applications and is popular in the aerospace, military, and defense spaces. This alloy is also used for many consumer products including keys and bicycle components, and sporting equipment.
7075 aluminum forging7075 Chemical Composition:
Si: ≤0.4
Fe: ≤0.5
Cu: 1.2-2.0
Mn: ≤0.3
Mg: 2.1-2.9
Cr: 0.18-0.28
Zn: 5.1-6.1
Ti: ≤0.2
Al: Balance
Properties of 7075 Aluminum Forging
Aluminum 7075 is the major forging alloy in 7000 Series and Zinc is the major alloying element in this series. Aluminum 7075 forgings possess high static strength and is used in airframe structures and for highly stressed parts. Aluminum 7075 forging is available in several types of tempers such as T6, T651, T73, T7351 and T76.
T6 temper has the highest strength but lowest toughness and resistance to stress-corrosion cracking. Since toughness decreases with a decrease in temperature, the T6 temper is not generally recommended for cryogenic applications. The T73 temper provides much improved stress-corrosion resistance over T6 temper with a decrease in strength. The T76 temper provides improved exfoliation resistance and limited stress corrosion resistance over T6 temper with some decrease in strength.
Applications for 7075 Aluminum Forgings
Commonly used in the manufacture of aircraft and other aerospace applications not requiring the corrosion resistance.
6061 VS 7075 Aluminum Forging
When it comes to the using of 6061 aluminum alloy or 7075 aluminum alloy for a forging project, understanding their differences and application ranges can go a long way and save you the trouble when looking to balance performance with cost. For most general purposes, both alloys may be able to get the job done but the differences in composition, mechanical properties and cost between both alloys can help you determine which of the two is the best choice for your forging needs.
6061 aluminum forging contains less zinc than its 7075 counterpart, meaning that while 6061 alloys provide superior workability over other alloys, it doesn’t boast the same high strength and stress resistance as 7075 aluminum forging.
General Mechanical Properties of 6061 Aluminum Forging
Tensile Strength – 45,000 psi
Yield Point – 40,000 psi
Brinell Hardness – 95
Elongation at Break – 12%
Shear Strength – 31,000 psi
Thermal Conductivity – 170 W/m-K
Strength to Weight Ratio: 115 kN-m/kg
General Mechanical Properties of 7075 Aluminum Forging
Tensile Strength – 83,000 psi
Yield Point – 74,000 psi
Brinell Hardness – 150
Elongation at Break – 10%
Shear Strength – 48,000 psi
Thermal Conductivity – 130 W/m-K
Strength to Weight Ratio: 196 kN-m/kg
100 | 2618 | 5083 | 6061 | 7079 |
2014 | 3003 | 5086 | 7039 | 7175 |
2024 | 4032 | 5383 | 7050 | |
2219 | 5052 | 5456 | 7075 |
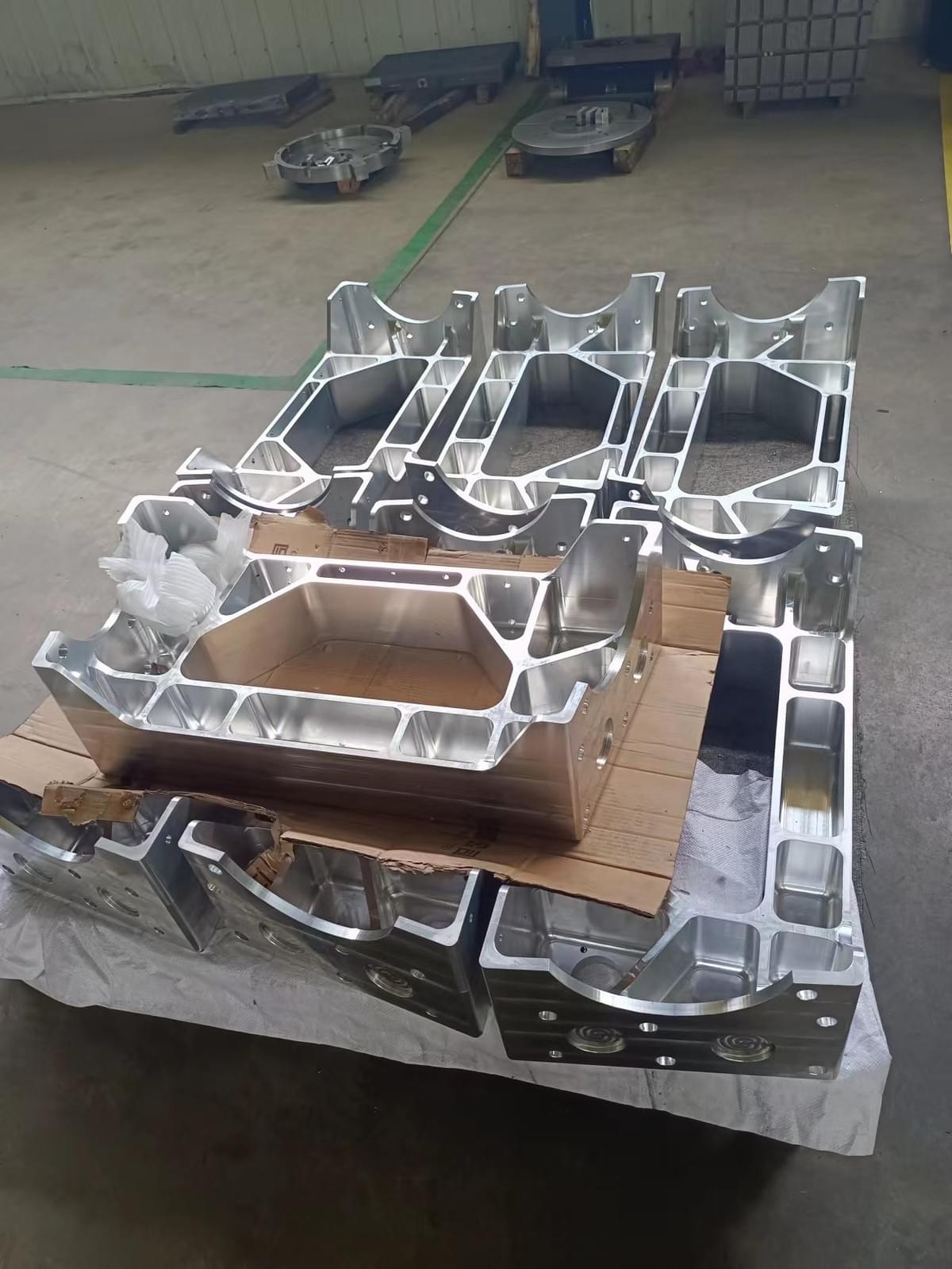
Anodization for Aluminum Forgings
Anodization or Anodizing treatment is the common surface finishing/coating method used for aluminum components, including aluminum castings, aluminum forgings, and even machined aluminum parts. Aluminum forged part is "anodized" for corrosion resistance, improved appearance, hardness & wear resistance, and for a number of specialized reasons like better glue-ability (adhesive bonding) for structural use, improved paint adhesion, and enhanced capacitance in electronic applications. Aluminum forgings are better than castings for anodizing due to a denser, more homogeneous microstructure. CFS Forge is the leading manufacturer for finished aluminum forgings, including closed die forging, cnc machining, surface finishing, heat treatment. So we can also deal with aluminum forgings that require further anodization. Here we introduce anodization for aluminum forgings in detail:
Process and Methods
There are normally four stages in the process: pre-treatment, anodising, colouring (where required) and sealing. The most frequent type of anodising is natural anodising. The electrolytic process takes place once the aluminum forging surface has received the appropriate mechanical or chemical pre-treatment and has been thoroughly cleaned.
Preparation before anodization includes processes of removing sharp edges, making smooth roughness, leaving certain machining allowance caused by thickness of the coating layer, designing special jigs, and protecting the not required anodizing surface.
We can general divide anodization methods for aluminum forgings into hard anodization and soft anodization.
hard anodizing for aluminum forgings
Hard anodizing is a thick film anodic oxidation process, which is a special anodized surface treatment process for aluminum forgings as well as other aluminum components. General thickness of hard anodized film is 40-70 um.
Advantages of Hard Anodizing for Aluminum Forgings:
The surface hardness of aluminum alloy forgings after hard oxidation can reach up to HV500.
The oxide film thickness is 25-250um.
Strong adhesion. according to the oxidation characteristics generated by hard oxidation: 50% of the oxide film penetrates inside the aluminum forgings and 50% is attached to the surface of aluminum forgings (bidirectional growth).
Good insulation: the breakdown voltage can reach 2000V (perfect seal).
Good abrasion resistance.
Non-toxic: Oxidation film and electrochemical process used to produce anodic oxide film should be harmless to human body.
Another anodizing method is soft anodizing, similar process with hard anodizing, just more colors and thinner thickness. This anodizing method is mainly used for decorative purpose. Common oxidation film thickness of soft anodizing treatment is 8 -- 12 um. And a lower hardness HV250-350 can be obtained.
soft anodizing for aluminum forgings
So, in order to reduce the weight of the product and protect the environment, many metal components are converted into aluminum forging with hard anodizing treatment, which were originally produced in steel forgings with hard chrome plating. More advantages of aluminum forging...
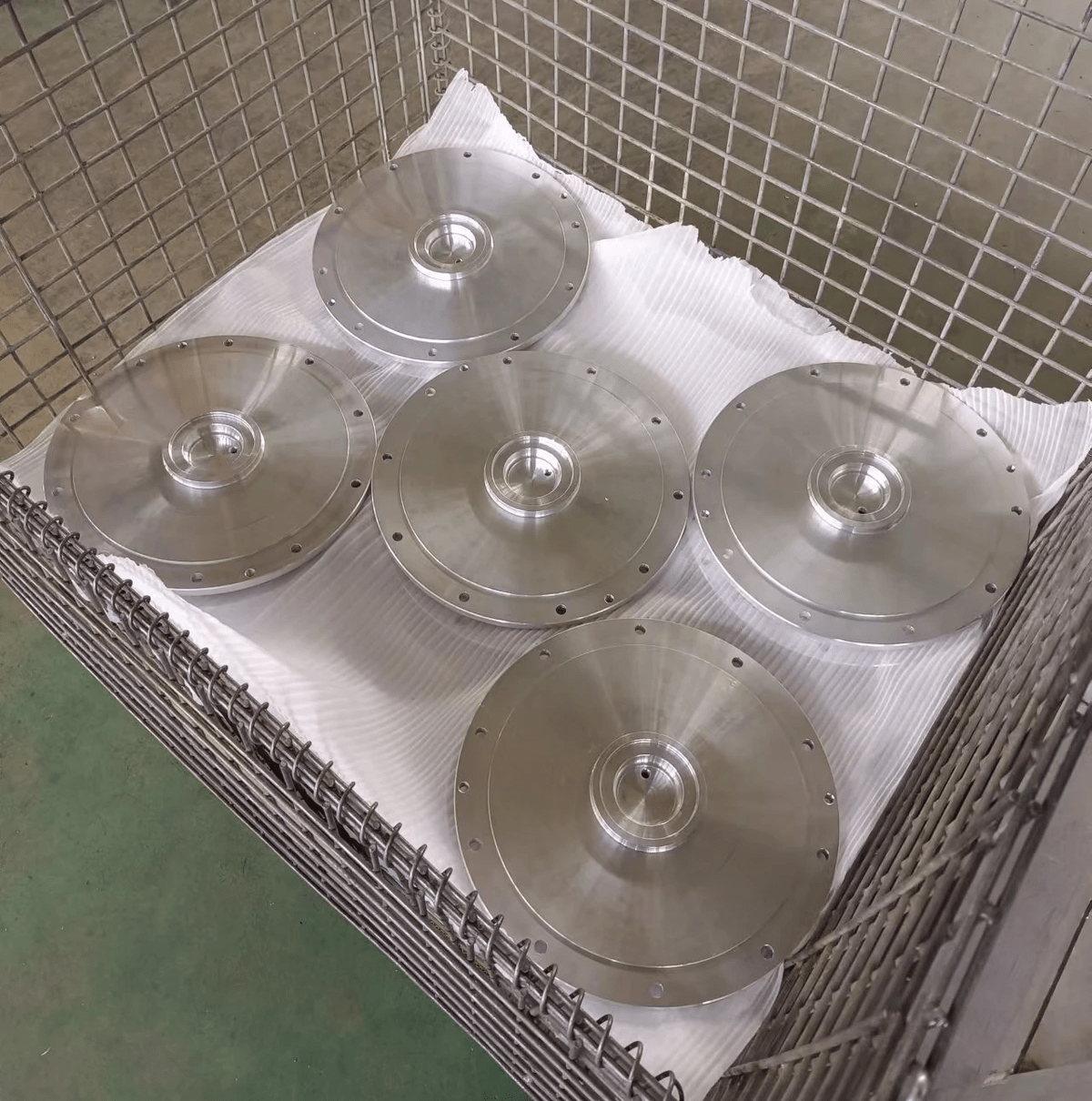
7175 7075 Aluminum Alloy Chemical Composition | |||||||||||||
Alloy | Si | Fe | Cu | Mn | Mg | Cr | Ni | Zn | Ti | Zr | Others | Al | |
Single | Total | ||||||||||||
7175 | 0.15 | 0.20 | 1.2~2.0 | 0.1 | 2.1~2.9 | 0.18~0.28 | ~ | 5.1~6.1 | 0.10 | ~ | 0.05 | 0.15 | Rest |
7075 | 0.40 | 0.50 | 1.2~2.0 | 0.3 | 2.1~2.9 | 0.18~0.28 | ~ | 5.1~6.1 | 0.20 | ~ | 0.05 | 0.15 | Rest |
Aluminum Forging introduction:
Forging is a metal manufacturing process with a long history. The advantage of forging production lies in that it can not only obtain the shape of mechanical parts, but also improve the internal organization of materials and improve the mechanical properties. Due to the excellent performance of aluminum and aluminum alloy, it has been widely used in machinery, electricity, electronics, automobiles, ships, construction, instrumentation, hardware and household products and other fields. Therefore, for important mechanical parts with high mechanical properties and large bearing capacity, they are mainly made by aluminum forging. The weight of aluminum forgings accounts for 77% in aircraft, 68% in tank and 76% in automobile.
Forging production occupies a very important position in the industrial industry, aluminum alloy is also the commonly used material in forging, all kinds of products that can be forged with low carbon steel can be replaced by aluminum forging. Most forged aluminum parts are safety parts and are produced in large volume, so there is a high requirement on internal quality of aluminum materials. Aluminum forging generally follows these manufacturing processes: blanking - heating - forging - heat treatment - machining. During the whole forging process, each procedure needs to be controlled carefully.
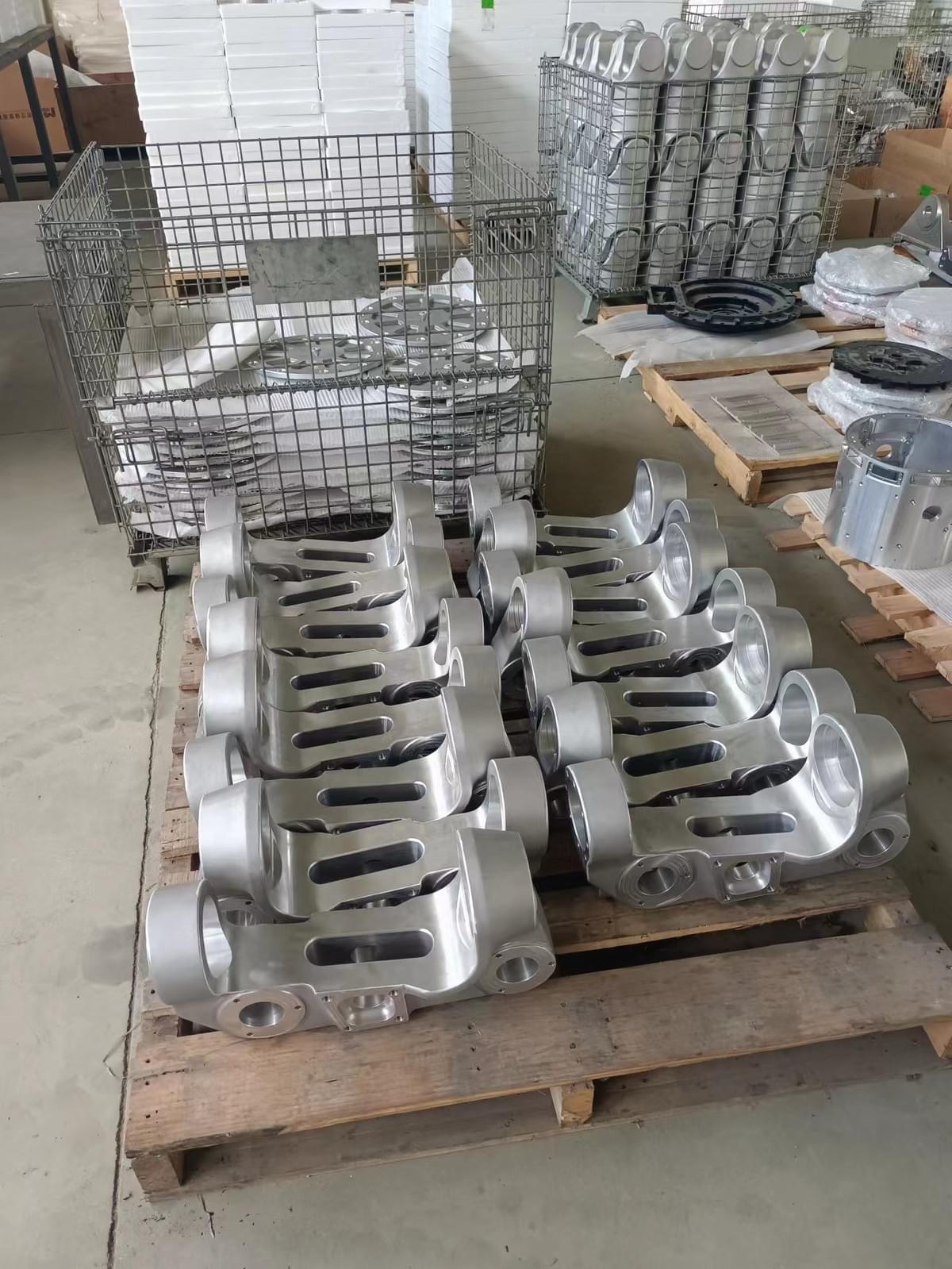
Technical Indicators for 7075 T74 Aluminum Alloy Forging | |||||
Direction | Rm/MPa | Rp0.2/MPa | A5/% | KIC/(N.mm-2).m1/2 | Conductivity/(MS.m-1) |
portrait | 490 | 420 | 9 | 33.0 | 22.6 |
Long transverse | 483 | 400 | 5 | 27.5 | |
Section transverse | 469 | 393 | 4 | 23.1 |
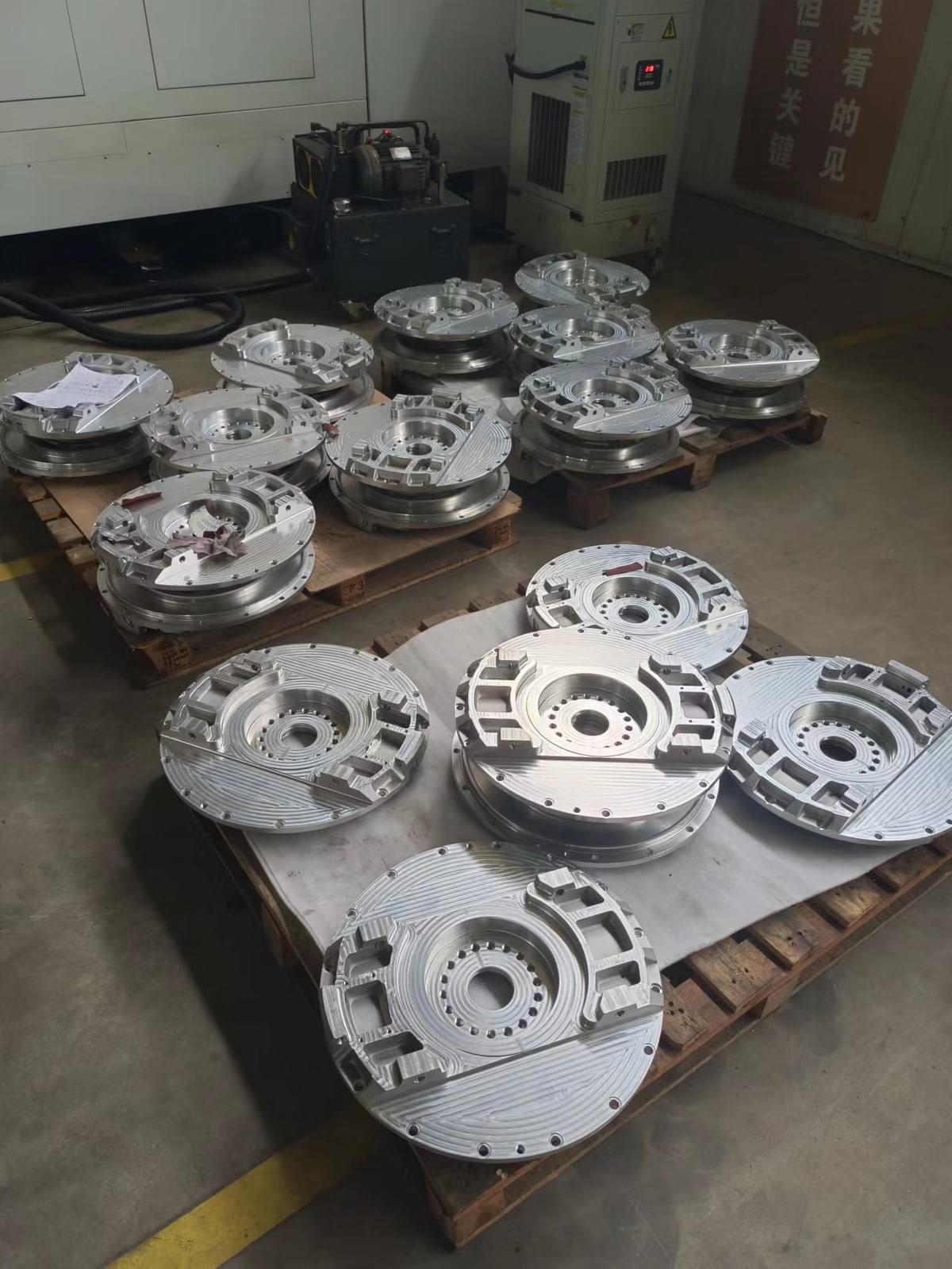
Aluminum alloys are produced by all of the current forging methods available, including open-die (or hand) forging, closed-die forging, upsetting, roll forging, orbital (rotary) forging, spin forging, mandrel forging, ring rolling, and forward and reverse extrusion. Selection of the optimal forging method for a given forging shape is based on the desired forged shape, the sophistication of the forged-shape design, and cost.
Most aluminum alloy forgings are produced in closed dies. The four types of aluminum forgings shaped in closed dies are blocker-type (finish forging only), conventional (block and finish forging or finish forging only), high-definition (near-net shape produced by forging in one or more blocker dies followed by finish forging), and precision (no draft, net shapes produced by forging with or without blocker dies followed by two or more finish forging steps in the finish dies). Blocker-type forgings are produced in relatively inexpensive, single sets of dies. In dimensions and forged details, they are less refined and require more machining than conventional or high-definition closed-die forgings. A blocker-type forging costs less than a comparable conventional or high-definition forging, but it requires more machining.
Conventional closed-die forgings are the most common type of aluminum forging. They are produced with either a single set of finish dies or with block-and-finish dies, depending on the design criteria. Conventional forgings have less machine stock and tighter tolerances than blocker-type forgings but require additional production costs, both for the additional die set and for additional forging fabrication steps required to produce this type. High-Definition Forgings. With the advent of state-of-the-art forging press and supporting equipment and enhanced forging process control, as are discussed below, high-definition, near-net-shape, closed-die forgings illustrated can be produced. High-definition closed-die forgings offer superior forging design sophistication and tolerances over conventional or blocker-type forgings and therefore enable even further reduction in final component machining costs. High-definition forgings are produced with multiple die sets, consisting of one or more blocker dies and finish dies, and are frequently used in service with some as-forged surfaces remaining unmachined by the purchaser.
Aluminum Forging Alloys:
There are lots of aluminum alloys can be used for drop forging. Main grades in aluminum forgings include: AL 6061, AL 6063, AL6082, AL 7075, etc.
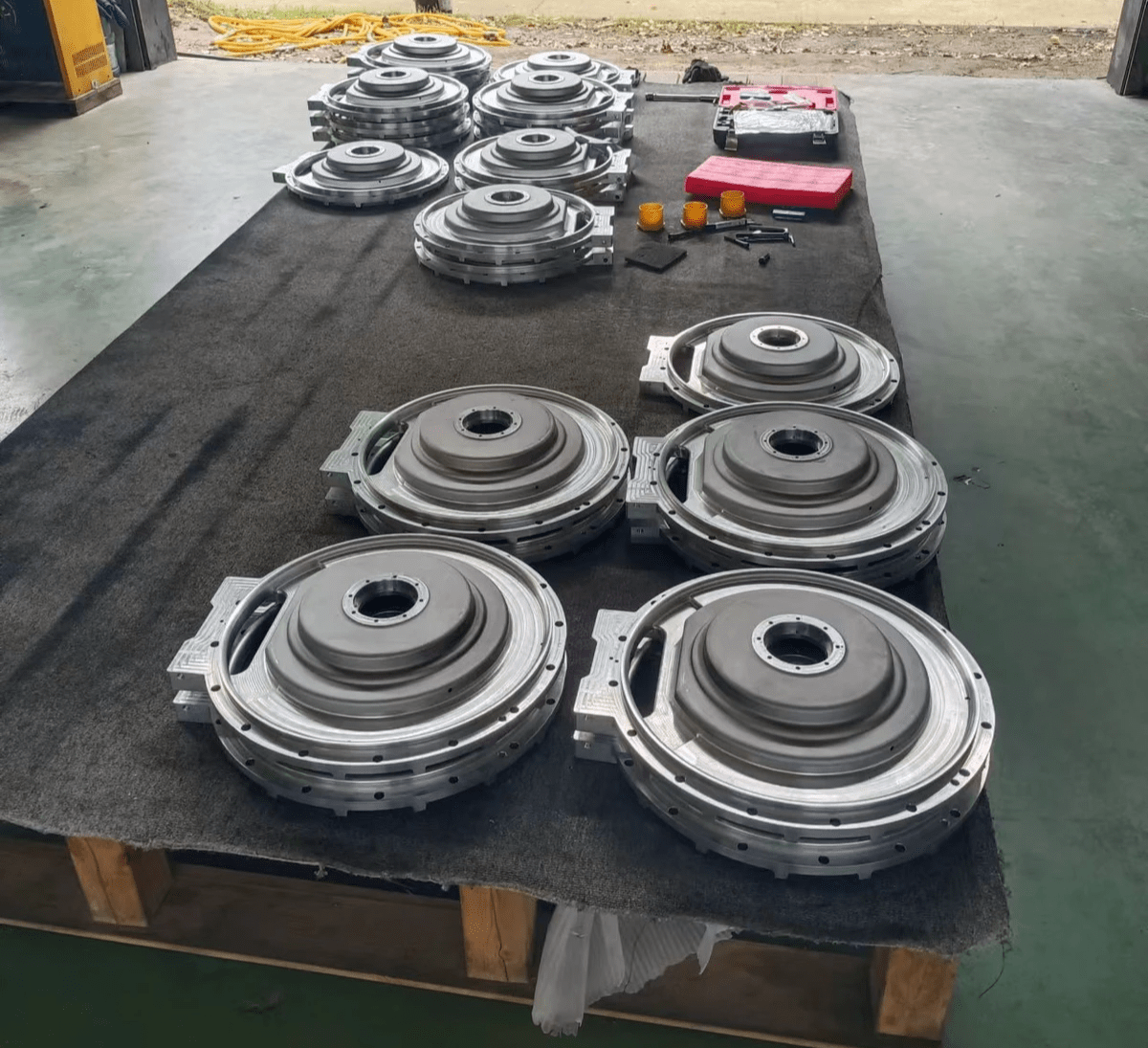
Difference Between Aluminum Forging Alloys and Aluminum Die Casting Alloys
First of all, forging and die casting are two kinds of different forming processes for aluminum alloy components. Based on different manufacturing methods, the aluninum alloys used are also different.
Aluminum forging alloys include A1--Si--Mg--Cu alloy and A1-Cu-Ni-Fe alloy, the commonly used aluminum forging alloys are 6061, 6063, 6082, 7075, etc. Their thermoplasticity is excellent, so the forging performance and mechanical properties are good. This kind of alloy is mainly used for making aluminum forgings that can bear the load and have complex shapes.
Aluminum casting alloys include four major categories: A1-Si alloy、A1-Cu alloy、Al-Mg alloy and Al-Zn alloy. For casting aluminum alloys, in addition to the necessary mechanical properties and corrosion resistance, they should also have good casting performance. In cast aluminum alloys, the best combination of casting properties and mechanical properties is A1-Si alloy.
By comparision, aluminum alloy forging can advoid defects caused by casting. What's more, the mechanical properties of aluminum forging are much better.
Aluminum Forging Benefits
There are lots of advantages in aluminum forging. First of all, as the internal organization of aluminum forging alloys is fine and uniform, they can be forged in various shapes with little to no machining allowance, which can greatly save labor cost and production time. Secondly, the thermal conductivity of aluminum forgings is good. Thirdly, forged aluminum parts have high density, no loose, pinhole, no air hole on the surface, with good surface treatment performance. In short, aluminum forgings has light weight, high strength, high toughness, excellent fatigue resistance and corrosion resistance, good thermal conductivity, easy to machining.
--- As an economic means of designing and making a shape. Machining can be eliminated and a high production rate can be achieved. Designs can be produced that eliminate the need for joints and welds.
--- A high strength to weight ratio can be achieved. The act of forging produces a fully wrought structure improving the shock resistance and fatigue resistance.
--- The surface finish is good and the elimination of porosity ensures pressure tightness. This combination of good mechanical properties, dimensional accuracy and surface finish means that aluminium forgings are used in highly stressed parts where structural integrity is of paramount importance. The alloys commonly used for these highly stressed applications are from the 2000, 6000 and 7000 series. The aerospace industry is a major end user.
Post Treatments of Aluminum Forging
Heat Treatment: T6 Heat Treatment
Like steel forgings, aluminum forgings may also require heat treatment to achieve a certain properties. T6 heat treatment is the typical heat treatment way after aluminum forging.
Heat treating of aluminum forgings depends to a great extent on the type and grade of aluminum forgings. Main purpose of heat treating stainless steel castings is to relieve stresses, improve mechanical properties or facilitate machining. The processes generally produce nearly uniform properties throughout the forging, and are not used for localized effects such as surface hardening.
Note: Before heat treating operation, surface cleaning is necessary performed on aluminum forging blanks to remove oils, grease, and other types of residue. Left on the aluminum forging surface during heat treating may affect the properties of products.
Post Machining
Although aluminum forgings after closed die forging process can achieve a higher size accuracy and surface finish, it does not mean machining can be saved for all the aluminum forged products. Machining will have to be performed when there is a closer tolerance and surface finish requirement that forging can not meet.
Our factory has built a reputation to do machining after aluminum forging. Our specialized machining services enables us to manufacture aluminum forgings with intricate geometry and detail, while maintaining high precision and accuracy. Our company has equiped with full sets of machining equipmement from manual turning & milling to complex CNC machining services. We offer the capabilities to machine aluminum forgings from several ounces up to 50lbs.
Inspection after machining is also very critical, we utilize manual inspection equipment and gages as well as the latest in coordinate measuring machine (CMM) technology to measure and record all the dimensions. This ensures our customers always get the quality they want.
Surface Treatments
Surface treatment or surface finish is very popular post treatment method to smooth the surface of aluminum forgings. See the types of surface treatment for aluminum forgings in below:
Shot blasting: | The most widely used surface treatment method used to clean, or polish the surface of stainless steel castings. Low cost. |
Sand blasting: | A kind of surface treatment that refines the surface of aluminum forgings. The surface smooth of sand blasting looks better than that of shot blasting, but higher cost. |
Anodization treatment: | Used to remove surface tiny burrs and improve the brightness of aluminum forgings. The surface looks smooth and a bit shining. |
Mechanical Polishing: | The most smooth and shiny surface treatment method, but costs high. |
7075 Aluminum Forging
Aluminum 7075 is the major forging alloy in 7000 Series and Zinc is the major alloying element in this series. Aluminum 7075 forgings possess high static strength and is used in airframe structures and for highly stressed parts. Aluminum 7075 forging is available in several types of tempers such as T6, T651, T73, T7351 and T76.
T6 temper has the highest strength but lowest toughness and resistance to stress-corrosion cracking. Since toughness decreases with a decrease in temperature, the T6 temper is not generally recommended for cryogenic applications. The T73 temper provides much improved stress-corrosion resistance over T6 temper with a decrease in strength. The T76 temper provides improved exfoliation resistance and limited stress corrosion resistance over T6 temper with some decrease in strength..
For the closed-die forging of aluminum components, die or mold is critical element in the overall aluminum forging process, because the dies are a major element of the final cost of such forgings. Further, forging process parameters are affected by die design, and the dimensional integrity of the finished forging is in large part controlled by the die cavity. Therefore, the forging of aluminum alloys requires the use of dies specifically designed for aluminum because:
The deformation behavior of aluminum alloys differs from that of other materials; therefore, the intermediate and final cavity die designs must optimize metal flow under given forging process conditions and provide for the fabrication of defect-free final parts.
Allowances for shrinkage in aluminum alloys are typically greater than those for steels and other materials.
Temperature control of the dies used to forge aluminum alloys is critical; therefore, the methods used for die preheating and maintaining die temperatures during forging must be considered in the design.
Artisan Industry is one of the largest aluminum forging company in China. We can supply custom forging and machining service ranging from 0.05kg-10kgs that match your exact design specifications with any aluminum grade required.
Why us?
Advanced Manufacturing Process & Fast Delivery: professional aluminum forging companies in China, all the production equipments used in our aluminum forging process are imported and checked regularly. Besides, we continuously study foreign advanced production experience to improve our strength. This will enable our customers to achieve superior quality, fast delivery.
Full Solution: factory is not only limited to aluminum forging, we also have the capabilities of heat treatment, post machining, surface treatment to supply finished products to our customers. What’s more, we can also supply redesign service for free if the design is not so ideal for aluminum forging production.