Artisan Industry,professional supply Aluminium lithium alloy material, Customized CNC machining service
Info@artisanmake.com WhatsApp+86 15050615346
Artisan Industry, which mainly focus on R & D,technology service,manufacture and sales of High performance non-ferrous alloy material and machining parts, Like aluminium alloy parts ,magnesium alloy parts, Copper alloy parts, Lead alloy parts, Zinc alloy parts, Master alloy parts, Deforming allo partsy, Military special alloy parts,Forgings and Castings,Extruded profile,etc.
Meantime,we are dedicated to global customers to provide a set of tailored high quality Non-ferrous alloy solution according customer’s requirement.which involves select material,material fusion cast process ,precision CNC Machining, link, surface treatment to the final parts of the whole process service.
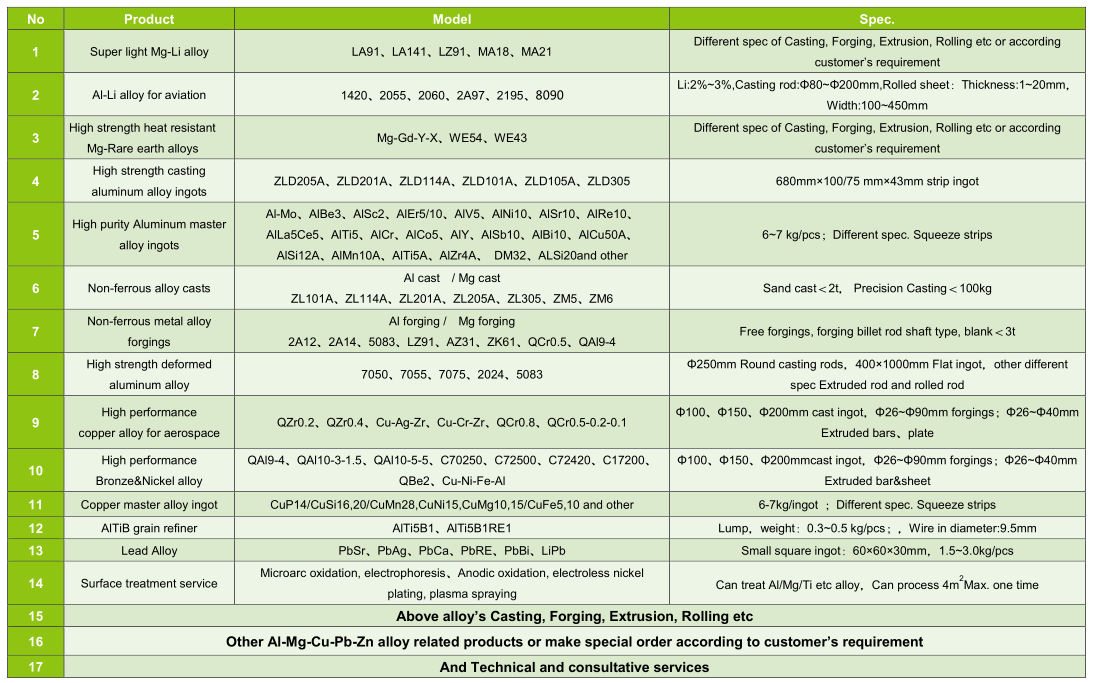
What is aluminum lithium alloy used for?
Image result for aluminum lithium alloy parts Aluminium Lithium finds use in aerospace and high-performance applications requiring high strength, low density, high stiffness, superior damage tolerance, excellent corrosion resistance, superior fatigue cracking resistance and weldability.
What are the advantages of Aluminium lithium alloys?
Al–Li alloys are lighter and have high tensile and yield strength compared to the conventional high-strength aluminium alloys. They are resistant to fatigue crack propagation; however, their corrosion resistance still needs to be improved.
What are the main drawbacks of Al Li alloys?
The accelerated growth of small fatigue cracks, strong anisotropy, poor short-transverse properties, and a sensitivity to compression overloads are the principal disadvantages of Al-Li alloys
Why is the aerospace industry so interested in using Al Li alloys?
The third generation of Al–Li alloys is considered as promising candidates for various components of aircrafts due to their excellent combination of low density, high strength, high stiffness, and excellent damage tolerance
Because lithium is the least dense elemental metal, materials scientists and engineers have been working for decades to develop a commercially viable aluminum-lithium (Al-Li) alloy that would be even lighter and stiffer than other aluminum alloys. The first two generations of Al-Li alloys tended to suffer from several problems, including poor ductility and fracture toughness; unreliable properties, fatigue and fracture resistance; and unreliable corrosion resistance.
Now, new third generation Al-Li alloys with significantly reduced lithium content and other improvements are promising a revival for Al-Li applications in modern aircraft and aerospace vehicles. Over the last few years, these newer Al-Li alloys have attracted increasing global interest for widespread applications in the aerospace industry largely because of soaring fuel costs and the development of a new generation of civil and military aircraft.
What is 2055 lithium aluminum?
Image result Billet 2055 Lithium/Aluminum Ar-15 Upper Receiver. Type Iii Hardcoat Anodized. Weighs 5.8 Oz. Advanced Lithium/Aluminum Alloy Is Lighter, Stronger, More Rigid, & Has Greater Corrosion Resistance Than Standard 7075 T6 Aluminum.
Aluminum-Lithium Alloys introduction
The advantages of aluminum-lithium alloys are numerous and include improved weldability, reduced density, and an improved modulus of elasticity and precipitation hardening.
When considering the stringent requirements of the aerospace industry however, certain properties still require improvement including overall strength and fracture toughness.
Table 1 lists the chemical composition of various Al–Li alloys that have been industrially produced over the past thirty years. The forerunner Al–Li alloy to be developed and used was the Al–Mg–Li–Zr alloy 1420. In this alloy, the beneficial effect of 50 wt.% Mg addition on solid solution strengthening and on improved weldability was combined with the advantages of reduced density, enhanced modulus and precipitation hardening provided by 2 wt.% Li addition. A trace addition of almost 01 wt.% Zr was made to control recrystallization and grain growth. Alloy 1420 was used in the MIG-29 aircraft fuselage in the form of welded structures in the early 1980’s and subsequently applied to passenger aircrafts.
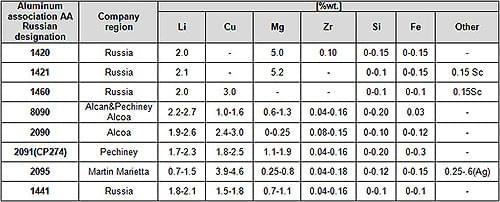
Table 1: Chemical composition of various industrial Al-Li alloys
However, the strength and fracture toughness of alloy 1420 were not adequate to meet the demands of modern aircraft, even in terms of specific properties. The reasons for poor fracture toughness, apart from those attributable to impurities, were related to shearing of the main strengthening phase δ’ (Al3Li) which led to planar slip – an aspect discussed in detail in the next section. Further research was therefore, directed towards compositions that promised additional non-shearable precipitates that would reduce the tendency for planar slip and lead to further hardening of the alloys.
As a result of the above, alloys such as AA 8090, AA 2090, AA 2091, 1441, 1460 were developed around the world. In addition to the δ’ precipitate, these alloys contained either one or both of the T1(Al2CuLi) and S (Al2CuMg) precipitate, that served to improve fracture toughness of these alloys.
Al–Li alloys have undergone several more changes in composition in the last ten years. First, the Li content of some of the alloys was reduced to < 2 wt.%. One such alloy, Weldalite-049 (AA2095), was developed specially for welded fuel tank applications. This alloy contained higher Cu compared to other Al–Li based alloys and derived its strength mainly from the T1 phase. In this alloy, Li helped improve the specific modulus.
The other alloy with lower Li content was the Russian sheet alloy 1441. Reduction in Li (< 2 wt.%) and Zr (=0.10 wt.%) content, combined with controlled rolling, allowed sheets to have fine equiaxed grain morphology, controlled texture and improved in-plane isotropy of properties.
More recent compositional changes have mainly focused on trace element additions like Ag, Ce, Y and Sc. Of these, Sc addition has been the most successful in microstructure refinement and improved microstructural stability at high temperatures. Some of the Sc-modified variants of alloy 1420 are produced commercially in Russia and used widely for welded applications.
According to previous experiments it was well documented that by aging of the supersaturated Al-Li (8091) solid solution, the maximum value of hardness (peak hardness) was achieved at this temperature. Reaching 190°C at pre-determined continuous heating, samples were water-quenched then cooled in liquid nitrogen in order in to prevent natural aging. Holding time at 190°C was 700 and 50min for samples heated at rates of 0.05 and 0.1oC/min, respectively.
Samples with dimensions 10x10x1mm were thinned by emery paper until the foil with a thickness of between 0.1 and 0.08mm was obtained. The disks with a diameter of 3mm punched from this foil were electrochemically polished. The polishing was performed at room temperature in the „Jet-pol“ apparatus using a mixture of 10% HClO4 and 90% ethanol, under the following conditions: voltage – 14V, current – 20mA, time of polishing – approximatelly 60s. TEM „JEM 100C–JEOL“used for microstructural examination was operated at 100kV.
A Vickers hardness with load of 10 kgf was applied to measure hardness of heat treated samples.
Quantitative microstructural analysis was carried out by a semi-automatic device for picture analysis with automatic data processing, using microphotographs produced by light and TEM. Structural parameters which best define processes and features were measured. They are primarily the parameters which characterize precipitated particles, i.e. the particle size, the volume fraction and the numerical density, as well as the distance between the particles.
Conclusion
Precipitation in the Al-Li (8091) alloy was studied during heating (0.05 and 0.1°C/min) from room temperature to peak hardness (190°C). Size, shape, density, distribution and other characteristics of precipitates were determined applying the method of quantitative metallographic analysis.
Precipitate identification performed by transmission electron microscopy (TEM) revealed the presence of strengthening phases formed during heating to 190°C: δ’ (Al3Li), S (Al2CuMg), and β’ (Al3Zr).
Very fine δ’ particles rather elliptic than spherical in shape together with lath shaped S phase may be seen in samples heated with both heating rates. Also, dislocation loops of various diameters are present in Al-matrix. The size of the δ’ particles are approximately 26% larger during the faster cooling rate.
With the lower heating rate, a higher hardness was obtained than in the case when the higher heating rate was applied. Higher values of hardness may be ascribed to the smaller size of δ' particles and their homogeneous and dense distribution in the Al matrix.
2070-T8E7 - ALUMINIUM LITHIUM ALLOY introduction
The alloy which is available in plate form is for high strength and damage tolerant applications where low density, high stiffness and excellent corrosion resistance is required.
The addition of lithium in the alloying process increases the strength and modulus of the material while lowering the density. Alloy 2070 aluminium lithium plates are available in thickness from 50.8mm to 165mm (2 to 6.5 inches), supplied in the T8E57 temper.
APPLICATIONS
Applications for 2070-T8E7 aluminium lithium plate include:
- RACING ENGINE COMPONENTS
- RACING ENGINE BLOCKS
- CHASSIS COMPONENTS
- STIFFNESS DOMINATED APPLICATIONS
- SUITABLE IN GEARBOX AND DRIVETRAIN DESIGN
TOUGHNESS & FATIGUE
Alloy 2070-T8E57 plate has shown comparable fracture toughness and fatigue (smooth and open hole) to the 7050 T7451 plate product. Fatigue crack growth in L-T and T-L orientations across gauges is generally improved compared to 7050 T7451 plate product.
CORROSION RESISTANCE
The material grade has shown excellent resistance to exfoliation corrosion and stress corrosion cracking in alternate immersion (ASTM G47) and seacoast environments.
BENEFITS
Benefits of using this alloy include:
- LOW DENSITY, HIGH STIFFNESS
- EXCELLENT CORROSION RESISTANCE
- SUPPLIED IN T8E57 TEMPER
- PLATE THICKNESSES FROM 50.8 TO 165MM
- FOR MOTORSPORT APPLICATIONS
aluminum-lithium materials advantage
Aircraft manufacturers are increasingly turning to lighter and stronger aluminum-lithium alloys, which are less expensive than other materials and enable better fuel efficiency and lower maintenance costs.
Lithium is the world's lightest metallic element. When alloyed with aluminum and other metals, the material provides an outstanding combination of strength, toughness, stiffness, corrosion resistance, and high-temperature performance, and at a lower cost than other materials.
lower the weight of single-aisle fuselage applications by up to 10 percent versus composites;
lower the cost to manufacture, operate and maintain planes by up to 30 percent versus composite-intensive airplanes, and at significantly lower production risk;
contribute to 20 percent better fuel efficiency; and
deliver passenger comfort features equivalent to composite-intensive planes, such as higher cabin pressure, large windows and higher humidity.
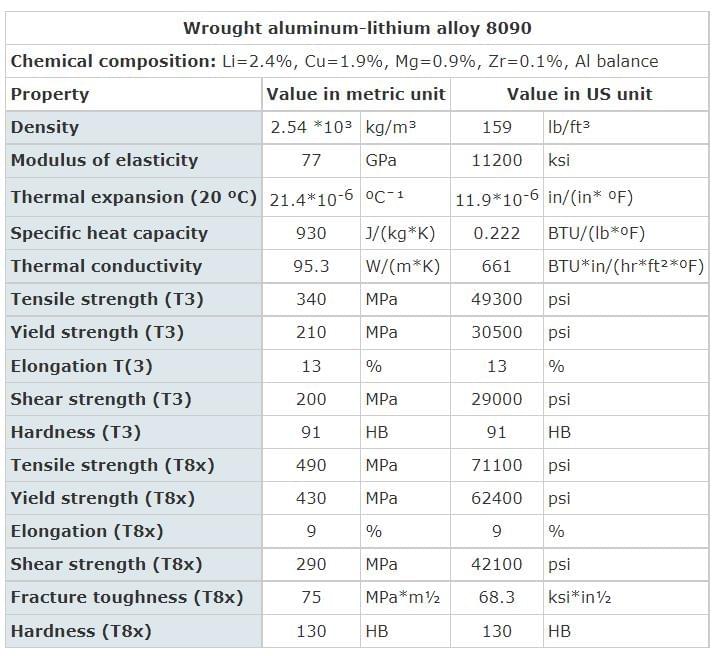
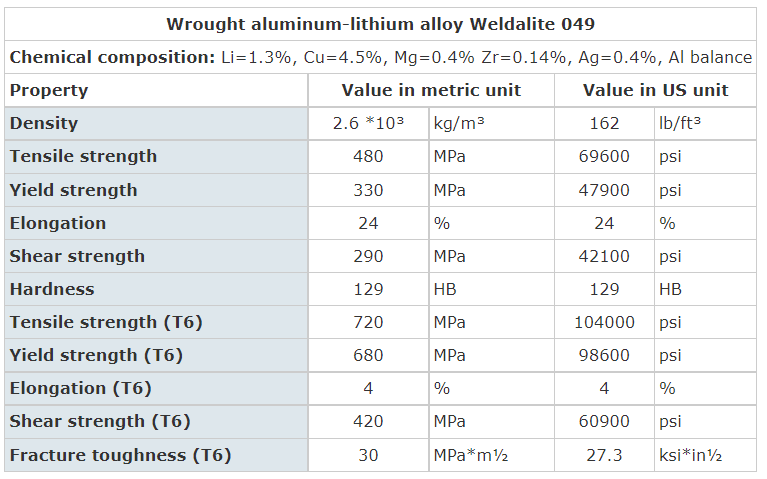
Wrought aluminum-lithium alloys
Dr. Dmitri Kopeliovich
Aluminum-lithium (Li) alloys were developed for reducing weights of aircraft and aerospace structures.
Aluminum-lithium alloys have decreased density because of very low density of metallic lithium 33.7 lb/ft³ (540 kg/m³). Addition of 1% of lithium results in decreasing density of the alloy by 3%.
Aluminum-lithium alloys may contain also copper (Cu), magnesium (Mg), zirconium (Zr) and silver (Ag) as minor alloying elements.
Aluminum-lithium alloys are heat-treatable.
Solution treatment followed by either artificial or natural aging allows considerable increasing the yield strength (3-5 times). Ductility of the alloy decreases as a result of the heat treatment.
Hardening of the alloys from this group is achieved due to precipitation of the phases Al3Li, Al2CuLi or Al2CuMg occurring during aging.
Aluminum-lithium alloys possess increased Modulus of Elasticity, high specific stiffness,increased fatigue strength and cryogenic strength. Alloys, containing silver, have also good weldability. Zirconium is added to aluminum-lithium alloys for controlling grain structure during heat treatment.
Aluminum-lithium alloys are used for manufacturing aircraft structures, aerospace vehicle skins, spacecraft fuel tanks (liquid Hydrogen and oxygen).
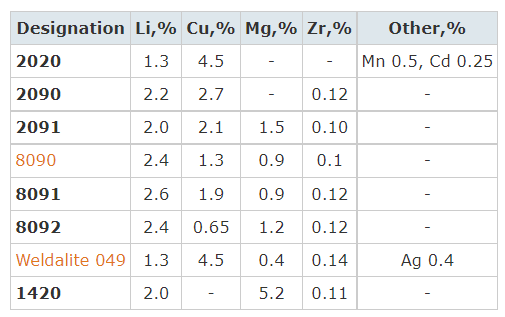