Common grades of stainless steel include:
-304 stainless steel
-316 stainless steel
-410 stainless steel
-430 stainless steel
-17-4 stainless steel
-Duplex stainless steel
Stainless steel precision casting is a manufacturing process used for producing a wide range of components from small components to large, complex parts. It can be used to produce parts with complex shapes and high levels of precision. Stainless steel casting is a versatile process that can be used to create parts with complex shapes and high levels of accuracy.
The stainless steel casting process begins with the creation of a mold, which is a negative image of the desired component. The mold is made from a wax or plastic material, and it is then filled with a liquid metal alloy. The alloy is heated to its melting point and then poured into the mold. As the metal cools, it takes the shape of the mold, forming the desired component.
Once the component has been cast, it is then machined or finished to the desired shape. This process may include grinding, sanding, or polishing to give the component its final shape. The component is then inspected for any defects or flaws and then finally sent for heat treatment. Heat treatment is done to harden the component and give it its desired properties.
Stainless steel casting is a great way to produce complex components with high levels of accuracy and precision. The process is relatively cost-effective and can be used to produce components in large quantities. It is also a great way to produce components with intricate details and shapes.
If you’re in the market for a stainless steel casting process, it’s important to do your research and find a reputable company to work with. Make sure to ask questions about their processes and experience in the industry, and don’t be afraid to ask for references. With the right company, you can be sure you’ll get the high-quality stainless steel components supplier you need.
Stainless Steel Castings manufacturer
Stainless steels refers to a family of metals which are primarily iron and contain more than 11% chromium by mass and varying percentages of nickel. Stainless steel alloys provide investment castings with high strength, corrosion resistance and operating temperature capability ranging from cryogenic temperatures to over 1500°F (816°C).
Stainless steel investment castings are fabricated by vacuum induction melting (VIM) of barstock followed by heat treatment. Stainless steel alloys can be weld repaired if required to repair casting defects or for in-service repairs.
Stainless Steel Castings are used in a wide variety of industrial, medical and aerospace applications where high strength and corrosion resistance are required up to moderate operating temperatures. Inconel alloys can be used for higher operating temperatures or more aggressive environments but at higher cost. Where lower strength is required, 300 series stainless steels can often be used at lower cost.
ph13-8Mo (13-8) Stainless Steel Castings possess excellent corrosion resistance that is comparable to Type 304 and Type 410 stainless steel castings. 13-8 stainless steel castings provide excellent resistance to oxidation at operating temperatures up to 1500°F (816°C). Long-term casting exposure to temperatures above 600°F (316°C) can result in reduced toughness.
Large Thin-Wall Casting Section
Large Thin-Wall Casting Section
15-5 Stainless Steel Castings are fabricated using a more recent metal chemistry variant of the older 17-4 stainless steel. 15-5 stainless steel is designed to provide greater toughness in thin casting sections by reducing delta ferrite formation. 15-5 stainless steel castings possess oxidation and corrosion resistance equivalent to that provided by 17-4 castings. Type 15-5 stainless steel is also known as UNS S15500, UNS J92110, AISI S15500.
17-4ph (17-4) Stainless Steel Castings are the most widely specified precipitation hardening stainless steel castings. Also called Type 630 stainless steel, 17-4 stainless castings maintain high strength up to operating temperatures of 600°F (316°C) and provide superior oxidation resistance compared to Type 410 stainless steel. 17-4 stainless steel castings possess corrosion resistance superior to the hardenable 400 series stainless steels and comparable to Type 304 stainless steel castings in most media. Type 17-4 stainless steel is also known as CB-7Cu-1, UNS S17400, UNS J92200, UNS S17480 and. UNS W37410.
300 Series Stainless Steels are the most widely used alloys for stainless steel castings.
Type 304 stainless steel castings are the most widely specified stainless steel castings. An austenitic stainless steel with 18% chromium and 8% nickel, Type 304 stainless steel castings can be used in non-corrosive environments or corrosive environments at temperatures up to 800°F (426°C). Type 304 stainless steel castings have excellent low temperature properties and retain high impact strength levels at temperatures as low as -400°F (-240°C). The higher chromium content compared to Type 316 stainless steels provides better high-temperature oxidation resistance. Type 304 stainless steel alloys are also known as CF8 and UNS J92600.
Type 304L stainless steel castings contain less than 0.03% carbon compared to less than 0.08% carbon in Type 304 stainless steel castings. The lower carbon content reduces susceptibility to intergranular corrosion in corrosive environments making solution annealed 304L castings suitable for some medical, industrial and chemical applications. Type 304L stainless steel castings are preferred compared to Type 304 stainless steel castings when the castings may require weld repair during services and post-weld heat treatment will not be performed. Type 304L stainless steel castings are used for service below 650°F (345°C). Type 304L stainless steel alloys are also known as CF3 and UNS J92500.
Type 316 stainless steel castings are fabricated from molybdenum bearing austenitic stainless steel making them more resistant to corrosion than Type 304 and 18-8 stainless steels. Type 316 stainless steel is a modification of Type 304 stainless steel with 2.0-3.0% molybdenum added to improve pitting and crevice corrosion resistance in chloride containing environments. Combined with higher nickel content than Type 304 stainless steel, Type 316 stainless steel castings provide improved mechanical properties at higher temperatures. Type 316 stainless steel alloys are also known as CF8M and UNS J92900.
Type 316L stainless steel is the low carbon version of Type 316 stainless steel. For maximum corrosion resistance, Type 316L stainless steel castings should be heat treated. Similar to Type 304L stainless steel castings, post-weld heat treatment is not required because the alloy’s low carbon content limits formation of significant amounts of chromium carbide in the weld heat-affected zone. Type 316L stainless steel castings have good machining and welding characteristics. Type 316L stainless steel alloys are also known as CF3M and UNS J92800.
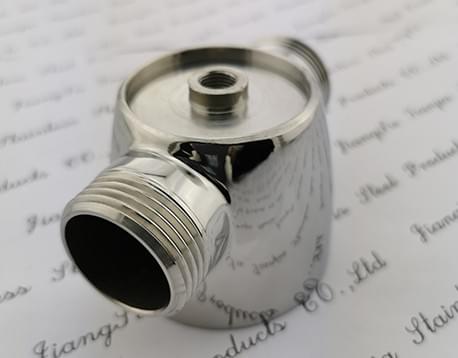